When it comes to the safety and durability of a smartphone, our minds go to screen protectors, software protection or casing material. But there is one key ingredient that is working in the background and is hardly noticed: the accuracy of the manufacturing molds that are used to form every part.
With the mobile devices getting thinner, lighter and more powerful, the necessity of structural integrity has been ever more pronounced. What then is the role of these invisible instruments of your device in its functionality and security?
The answer lies in the world of high-precision mold parts—the unsung heroes that define how every cell phone case fits, functions, and lasts.
What are High Precision Mold Parts?
High precision mold parts These are complexly designed parts of the mold making process when manufacturing plastic, metal, or composite parts. They establish the form, size, texture and mechanical soundness of the end product. These mold parts play a critical role in mobile manufacturing in the creation of consistent and durable components- particularly in high volume manufacturing environments.
These mold parts are manufactured via CNC machining, electrical discharge machining (EDM) and sophisticated polishing processes and can be produced to dimensional tolerances of a few micrometers. This precision will mean that each phone component, be it a casing, a button or a frame will be a perfect fit to the intended specifications. Any deviation, no matter how small, might cause parts that do not fit, snap out of place, or wear unevenly.
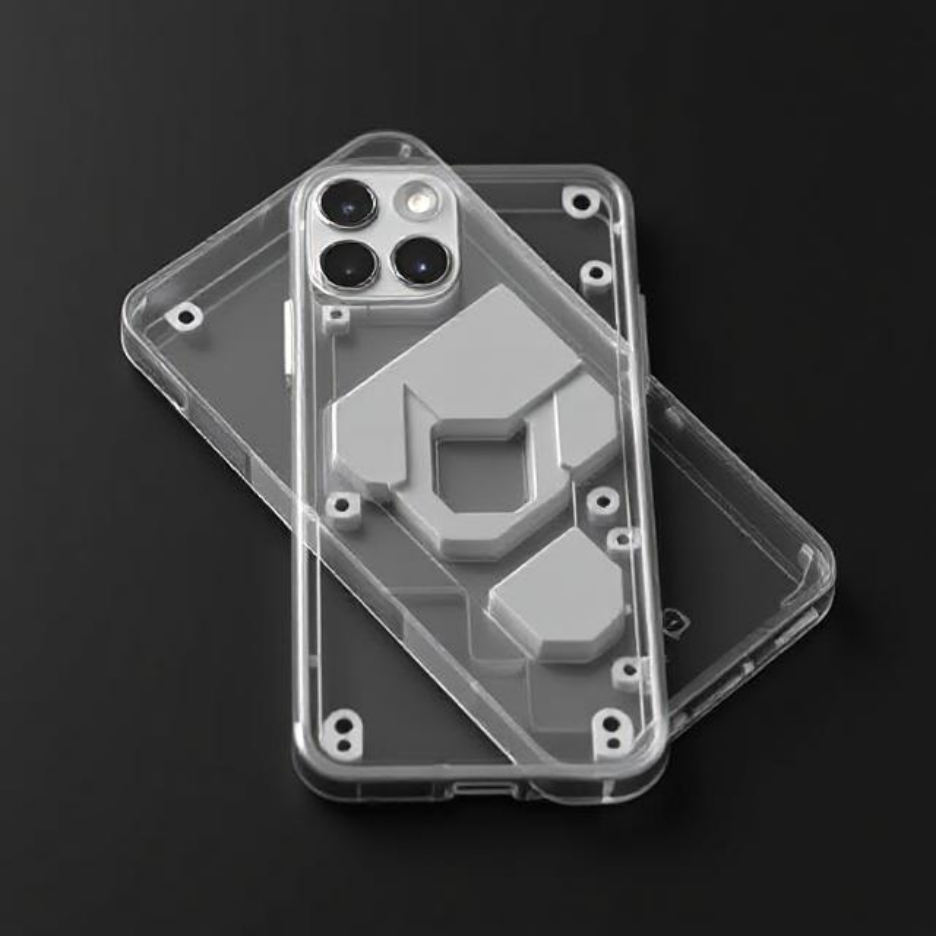
The materials that are employed in high precision molds need to withstand high temperatures and pressures and they should maintain their shape through thousands of cycles. Typical options are the tool steels, tungsten carbide, and even ceramic composites. Such molds are repeatedly subjected to loads to ensure durability and reliability.
How High-Precision Mold Parts Shape the Cell Phone Case?
The cell phone case is far more than a decorative shell—it plays a central role in protecting internal components, absorbing shock, and supporting heat dissipation. All the curves, edges, the opening of ports in that case are characterized by a mold. And it is the high-precision mold parts that make the difference in a unit to be able to meet the design expectation.
Any small defect in the mold during injection molding can lead to gaps, burrs or structural weaknesses. Those dangers are removed by high-precision mold parts that provide perfect symmetry and repeat dimensions at thousands of production cycles. A tight fit of a SIM card tray, a side button click, camera openings alignment all require that the mold be accurate.
This accuracy is even more important in the case of thin-walled design or complex geometries. Manufacturers rely on high-precision cores, cavities, sliders, and ejector pins to form every detail of a cell phone case. Cooling channels are also advanced to control temperature gradients in molding in order to enhance the stability of shapes.
Finally, as with any product, the structural integrity of the case, i.e. its resistance to bending, warping, and cracking, begins with the precision of the mold. The case, without it, may collapse under physical pressure and thus aesthetics and safety are compromised.
The Manufacturing Connection: Mold Accuracy and Smartphone Reliability
The current smartphones are designed to withstand uninterrupted usage, handling, and falling. Their reliability with time, as well as the integrity of their design, is directly connected with how accurately their parts are manufactured. In this regard, high precision mold parts act as the foundation of quality production.
With tight tolerances, assembly lines are more efficient and run faster. The cases, screens and internal parts snap on without any manual adjustments. This is not only more efficient in manufacturing but also less likely to cause component misalignment which can impair antenna performance, speaker output or even battery location.
A well-fitted cell phone case made using accurate mold parts also minimizes the entry points for dust and moisture, two key threats to internal circuitry. This is important in attaining water and dust IP ratings. In addition, the accuracy of internal structures made by the molds leads to improved thermal management. Cooling solutions are also built into the case such as heat-dissipating features that are molded into the case to provide enhanced cooling without additional hardware.
Concisely, mold accuracy influences the quality control to the end-user experience. The more the fit, the less the points of failure- resulting in longer lasting devices with high performance and safety standards today.
Future Trends in Mold Technology and Mobile Device Safety:
The smartphones are also changing and so should the technologies that they are being shaped by. The future of the high-precision mold parts is on the path of even higher precision, more intelligent automation, and compatibility with the digital manufacturing system.
The application of simulation software and digital twins in mold design is one of the major trends. Today engineers are able to simulate thermal behavior, material flow and structural stress without creating a physical mold first. This leads to better mold layouts, fewer design iterations, and higher production reliability—especially for complex components like the cell phone case.
Micro-molding is another development in which parts are extremely precise and are of the smallest size and high tolerances. This will be even more significant as devices become smaller and more sensors, cameras and biometric modules are being added to them in small spaces.
Hybrid molds, which have 3D-printed metal inserts to allow bespoke cooling channels or surface texture treatments, are also becoming more popular. These hybrid systems enhance the surface quality and minimise warping, which directly leads to strengthening and appearance of the final product.
Finally, precision molds will help to enter the production of biodegradable or recycled-material-based phone cases with the same performance rating as the current ones. Even with the eco-friendly plastics, consistency in material behavior will only be realized when there are mold parts that are engineered to specifications.
Conclusion:
High precision mold parts form the basis in the search of smarter, sleeker, and safer smartphones. From shaping the cell phone case to influencing structural integrity and long-term performance, their impact runs deeper than what meets the eye. The capability to create precise, dependable parts will be important as manufacturing requirements increase and design tolerances tighten. Accuracy is not an attribute, it is the mobile safety and innovation of the future.