In an era dominated by single-use plastics and rising environmental concerns, the ability to recycle effectively is more critical than ever. We’ve all heard about the massive floating garbage patches in the ocean and the alarming statistics about plastic pollution. But behind the scenes, industrial machines are quietly playing a heroic role in this story—transforming plastic waste into reusable material.
This article will delve into the scientific principles behind plastic recycling, as well as modern equipment such as advanced crushers and granulators. Let’s see how to change the way we manage plastic waste.
The Problem with Plastic: Built to Last, Not to Disappear
Plastic is everywhere because it’s cheap, durable, and lightweight. But that’s also the problem. Unlike organic materials, plastics are synthetic polymers that don’t decompose easily. A typical plastic bag can take up to 500 years to break down.
This durability means that without proper recycling systems, plastic continues to accumulate in landfills and waterways. That’s where science and technology step in.
The Science of Mechanical Recycling
Most industrial plastic recycling today relies on mechanical recycling—a process that physically transforms waste plastic into reusable raw material without altering its chemical structure.
Here’s a simplified version of how it works:
- Collection & Sorting – Plastics are gathered and sorted by type (e.g., PET, PE, PVC).
- Crushing & Shredding – Waste is reduced into smaller flakes using machines.
- Washing & Drying – These flakes are cleaned to remove contaminants.
- Melting & Pelletizing – Clean flakes are melted and reformed into pellets.
- Re-use – The pellets are used to manufacture new plastic goods.
Each step depends on reliable machinery—especially the first and last ones.
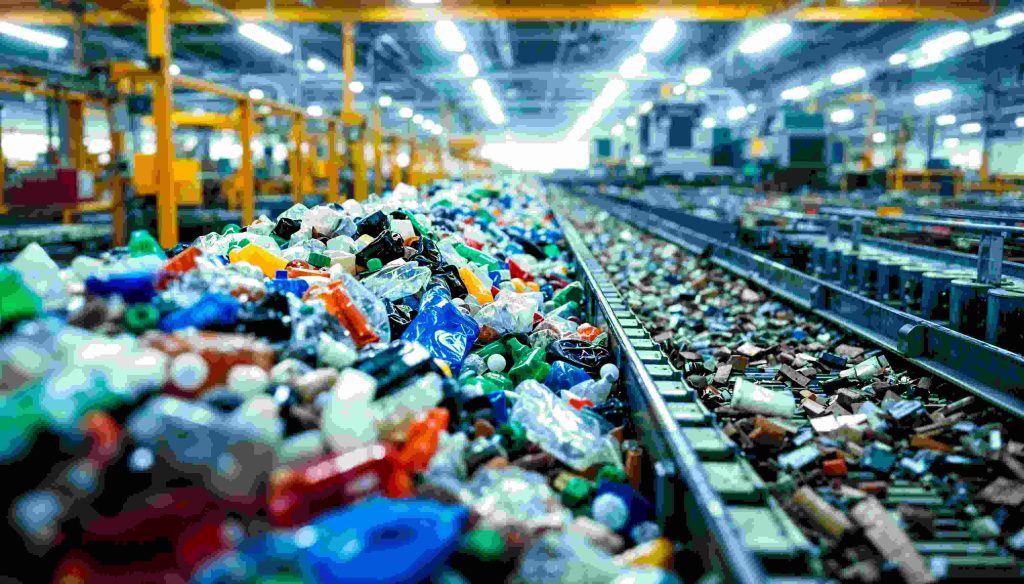
Crushing: Where Recycling Begins
The recycling journey often starts with crushing, where large pieces of plastic are reduced to small, manageable flakes.
Designed to handle a wide range of materials—from rigid PP and PE to more flexible PET and ABS—this crusher is ideal for plastic pipes, containers, packaging films, and much more.
Key features include:
- High-torque shredding for tough plastics
- Optional metal separator and conveyor feeding system
- Easy maintenance and CE-certified safety design
This type of industrial-grade crushing machine helps streamline the recycling process by improving efficiency right from the start.
Cleaning and Preparing the Flakes
Once the plastic is shredded, it’s washed thoroughly. Oils, labels, adhesives, and even dirt can compromise the quality of recycled plastic. Washing tanks and centrifugal dryers are used to clean the flakes until they’re ready for reprocessing.
Low-Temperature Granulation: Smarter Melting
Not all plastics can be melted the same way. Some—like TPU, PLA, or EVA—are heat-sensitive and degrade easily. That’s where low-temperature extrusion granulators come in.
Benefits include:
- Reduced material degradation
- Lower energy consumption
- Versatile compatibility with a wide range of polymers
By using this technology, businesses ensure higher-quality recycled output that’s suitable for everything from eco-packaging to textile fibers.
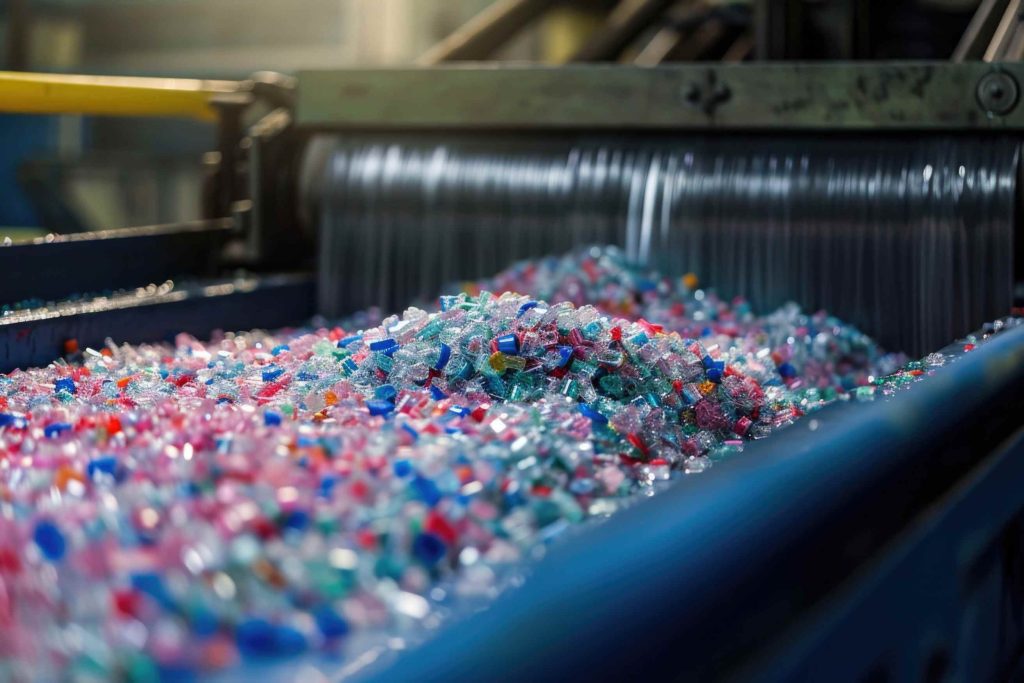
The Numbers Don’t Lie
Let’s put things into perspective:
- Smart control systems for real-time monitoring
- Safety interlocks and overload protection
- Energy-efficient motors and modular components
These improvements reduce downtime, cut electricity costs, and improve worker safety—all while contributing to sustainability goals.
Closing the Loop
Plastic recycling is no longer just an environmental responsibility—it’s a core business strategy. From waste reduction and cost savings to customer loyalty and regulatory compliance, the benefits of investing in industrial-grade recycling equipment are compelling.
So the next time you toss a bottle into a recycling bin, remember: behind that simple act is a global chain of innovation.