Lightweight and strong materials are significant in the modern manufacturing scene and are useful in all industries, including furniture and car designs. One such material is PU foam, or polyurethane foam. It is a versatile polymer prized for its cushioning, insulation, and structural properties. Yet, behind the production and reprocessing of this ubiquitous material lies a high-performance workhorse: the pulverizer machine.
The equipment allows not only size reduction of foam, but also recycling and formulation accuracy. What then is the interaction between these two elements of manufacturing ecosystems, material and machine? So, what is the science behind the connection of polymer chemistry and industrial pulverization?
PU Foam: Composition, Properties, and Industrial Use
PU foam, short for polyurethane foam, is a cellular polymer material formed through the reaction of polyols and isocyanates. This leaves a skeleton-like structure, that is, a lightweight structure full of gas cells, which gives it the cushioning and insulating effects it is known to possess. Depending on its formulation, PU foam can be rigid or flexible, making it suitable for a wide range of applications.
Flexible PU foam is widely used in furniture, mattresses, footwear, and automotive seating due to its shock-absorbing nature. Rigid PU foam, on the other hand, is employed in construction and refrigeration for thermal insulation. Other additives like flame retardants, plasticizers as well as stabilizers are added to tailor its mechanical as well as thermal characteristics.
Despite its usefulness, PU foam poses challenges in waste management due to its cross-linked molecular structure, which resists melting and reshaping. As a result, recycling requires mechanical size reduction—where technologies like the pulverizer machine become indispensable.
In modern industry, PU foam is not only a product but part of a broader materials ecosystem that demands both efficient production and sustainable end-of-life handling.
Pulverizer Machine: Operating Principle and Application in Polymer Processing
A pulverizer machine is designed to grind, crush, or pulverize materials into fine particles. In polymer processing, particularly with materials like PU foam, pulverizers play a critical role in enabling material reuse, improving formulation uniformity, and preparing granulated input for further molding or extrusion.
The majority of polymer pulverizers incorporate high-velocity rotors, stationary blades and sieves. The substance is introduced into a chamber wherein it is broken down by mechanical shearing and impact forces to form powder or flakes. For soft, spongy materials like PU foam, specialized low-temperature pulverizers are used to prevent heat-induced degradation during grinding.
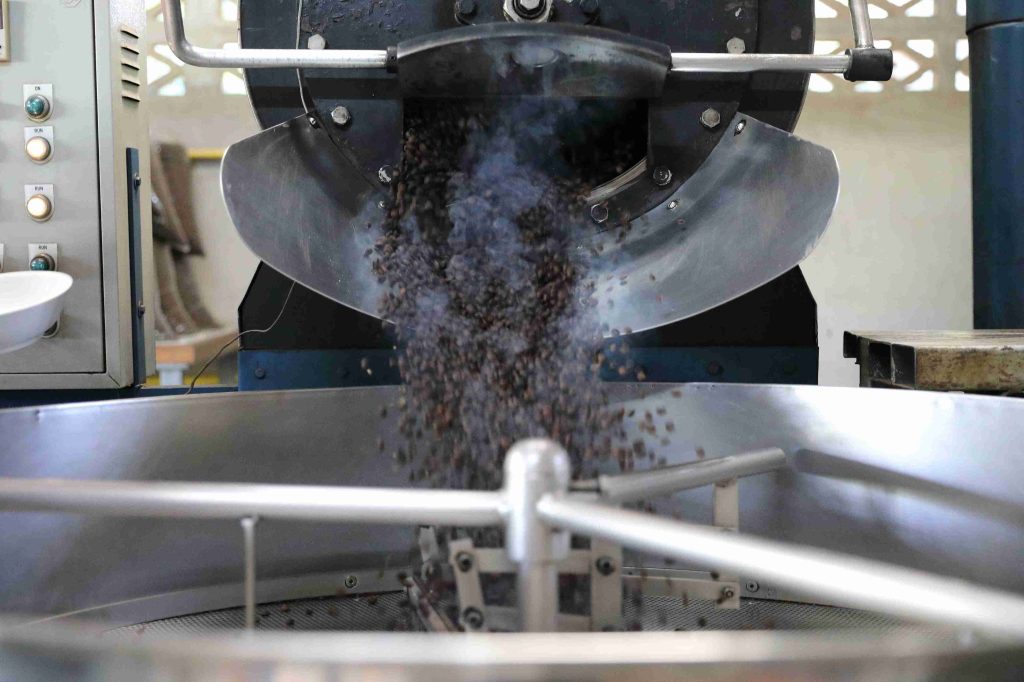
In PU foam recycling, the pulverizer machine helps convert post-industrial or post-consumer foam into regrind, which can then be mixed with virgin resin to produce rebonded foam sheets, mats, or molded components. Precision in particle size is essential—too coarse, and the regrind won’t mix well; too fine, and the material may degrade.
Modern pulverizers include features like digital temperature controls, nitrogen cooling systems, and vibration-reduction platforms to maintain consistent quality, throughput, and operator safety.
The Interface: How Pulverizer Machines Enable Circularity in PU Foam
As industries pivot toward sustainability, the integration of pulverizer machines into PU foam production and recycling lines is becoming increasingly common. These machines enable the manufacturers to form circular loops, in which waste foam is recycled into the production process.
In recycling setups, PU foam scraps—whether from furniture manufacturing, automotive upholstery, or insulation boards—are collected and fed into a pulverizer machine. The resulting powder can be utilized as the filler of the composite foams, or can be bonded using adhesives to create new structural products. Some also permit mixing pulverized PU with other polymers to make hybrid materials.
The compatibility of materials is important. PU foam’s open-cell or closed-cell structure affects how well it grinds and how it reintegrates. Adjustable rotor speeds and the various screen sizes of pulverizers allow the versatility required to process a variety of foam densities and shapes.
The combination of PU chemistry and state-of-the-art pulverization enables manufacturers to save the cost of raw materials, in addition to diverting great waste out of landfills. The synergy between pulverizer machine performance and PU foam recyclability exemplifies how mechanical and chemical engineering can support sustainable innovation.
Material Behavior Under Stress: The Science of Grinding PU Foam
PU foam is notoriously difficult to pulverize due to its elastic and compressible nature. The mechanical stress behavior of the material is very important in pulverization. When compressed, PU foam absorbs energy rather than fracturing, which is why standard crushing methods are inefficient.
The pulverizer machine overcomes this by utilizing high-speed rotors that slice the material into smaller fragments with shear forces. In some setups, cryogenic grinding is applied—PU foam is cooled with liquid nitrogen until it becomes brittle, allowing easier size reduction.
This produces granules with desirable properties like the integrity of the polymer chains and chemical stability. Caution is however needed to ensure that overheating is not experienced as this will result in degradation of the polymers and result in poor performance of the final product.
Pulverizers can manipulate final granule size and shape through precision in the alignment of blades, control of air flow and technology of separating particles. This control is particularly needed during the reintroduction of regrind into new formulations of PU due to the ability of inconsistencies to impact on the expansion of foam, density and homogeneity.
From a materials engineering perspective, the pulverizer machine doesn’t just crush—it respects the properties of polymers while preparing them for renewed life.
Smart Manufacturing: Digital Controls and Energy Optimization
Modern pulverizer machines are no longer standalone mechanical systems—they are intelligent components of Industry 4.0 production lines. These automated machines currently have programmable logic controllers (PLCs), touch-screen human machine interfaces (HMIs) and cloud connectivity to real-time monitor and optimize the machines.
For PU foam processing, temperature and particle size are critical parameters. Smart pulverizers are able to change blade speed, grinding pressure as well as the feed rate according to the material fed in it so that the results are similar in different batches. Built in sensors are used to measure blockage or temperature highs, such that automatic shut offs occur to protect the system.
Another great development is energy efficiency. Variable-frequency drives (VFDs) allow power savings during idle or low-load conditions. Other systems recapture heat produced in the grinding process and apply it in preheating the incoming material.
Installing a pulverizer machine into smart workflows enhances traceability, can reduce downtime, and can support predictive maintenance. When applied to PU foam production and recycling, this level of control transforms a once-wasteful process into a finely tuned, data-driven system.
Conclusion:
The combination of PU foam’s functional versatility and the pulverizer machine’s precision grinding capabilities has unlocked new possibilities in modern manufacturing. Whether it is more comfortable and well-insulated buildings, or the recycling and support of circularity, technologies overlap in the core of industrial innovations.
With rising demand for lightweight, eco-conscious materials, the ability to reuse and reform PU foam is no longer optional—it’s essential. Pulverizer machines offer the control, efficiency, and reliability needed to make this vision a reality.