Walk into any supermarket, warehouse, or shipping facility and you’ll see plastic in every corner of our modern world. From packaging film and food containers to pipes and car parts, plastics make up a vast portion of the products we rely on daily. But what happens after those items are used? Where does the plastic go? And more importantly, how is it transformed into something new?
The answer lies in the often-overlooked science of plastic recycling—a discipline where chemistry, engineering, and industrial design intersect to solve one of the 21st century’s biggest environmental challenges.
The Chemistry of Plastic Recycling
To understand how recycling works, you first have to understand what plastic is. Plastics are made of polymers—long chains of repeating molecular units that form strong, lightweight, and versatile materials. But these polymers vary greatly. For instance:
- PET (Polyethylene Terephthalate) is used in water bottles.
- PE (Polyethylene) is found in plastic bags and containers.
- PVC (Polyvinyl Chloride) is used in pipes and flooring.
- EVA, PLA, TPU and other modern materials are found in everything from packaging to wearable devices.
Each type behaves differently under heat, pressure, and mechanical stress. That’s why recycling isn’t a one-size-fits-all process. It’s a carefully calibrated system that begins with sorting, continues with crushing, and ends in reformation.
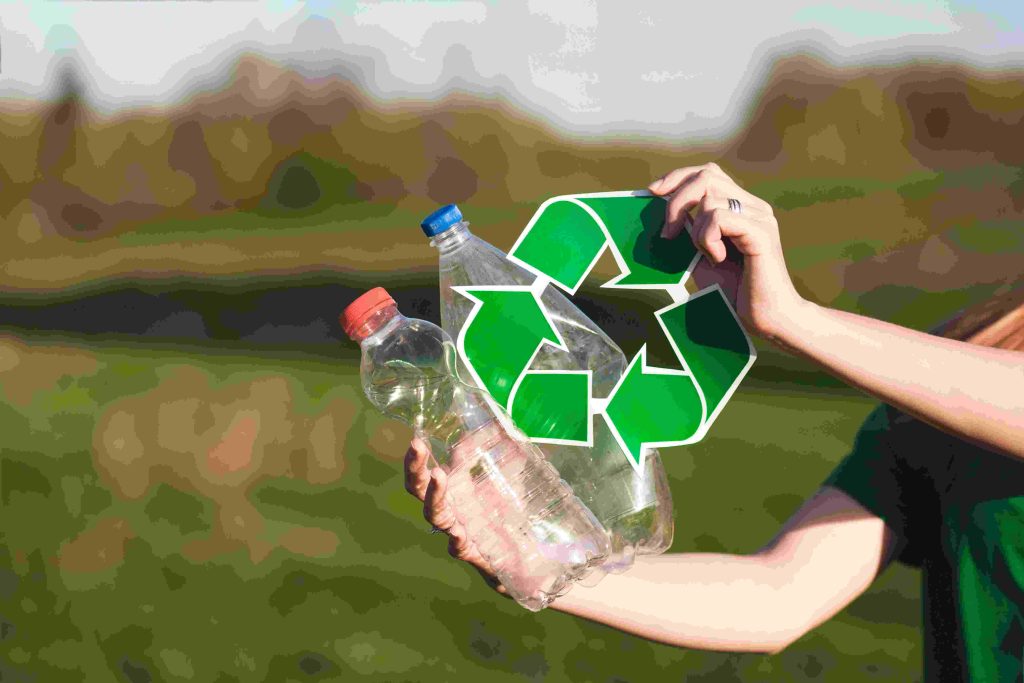
Step One: Mechanical Breakdown
The first step in any recycling plant is mechanical size reduction. Waste plastic must be broken into smaller, more manageable pieces before it can be washed or melted.
This is done using industrial plastic crushers and shredders, which feature powerful rotors and blades to crush everything from rigid PVC pipes to soft film and multilayer packaging. These machines reduce plastic to flakes, increasing the surface area and preparing the material for washing.
Many facilities also use metal separators and belt conveyors alongside these crushers to remove unwanted debris and streamline material flow. In high-efficiency recycling lines, these machines operate continuously and with minimal downtime, processing several tons of plastic per hour.
This crushing stage may seem mundane, but it’s vital. Inconsistent flake size can lead to uneven melting, degraded product quality, and unnecessary energy waste down the line.
Step Two: Cleaning and Sorting
Once the plastic is crushed, it’s washed. Residues like food grease, ink, and adhesives must be removed. This phase involves cold or hot water washing, sometimes with the help of detergents and friction washers.
Density separation tanks may also be used. Lighter plastics float, while denser materials sink—allowing operators to isolate types like HDPE from PET. The end goal is a clean, uniform plastic flake suitable for remanufacturing.
Here, modular recycling systems that combine shredding, cleaning, and drying in one continuous process offer a major advantage. They reduce handling time and help facilities meet stricter contamination limits required by high-end manufacturers.
Step Three: Thermal Reprocessing
Clean flakes are then melted and reformed into small pellets known as “regrind” or “regranulate.” These pellets can be fed into molding machines to create new plastic products.
However, not all plastics can handle the same temperature. Overheating can cause polymer chains to break down, reducing tensile strength and elasticity. This is especially true for low-crystallinity polymers like EVA, TPU, or biodegradable PLA.
To preserve the material’s integrity, modern recycling lines are increasingly using low-temperature granulators. These machines operate at lower processing temperatures with tighter control over thermal profiles, enabling the production of higher-quality regranulates.
In industries where product performance is critical—like automotive parts, medical packaging, or agricultural films—this precision matters. Granulators with integrated temperature feedback systems ensure consistent output with minimal polymer degradation.
Smart Recycling: Data Meets Durability
As industries evolve, recycling machines are becoming smarter. Sensors, PLC controls, and networked systems now allow facilities to monitor:
- Energy consumption
- Output rates
- Material types processed
- Maintenance schedules
Some systems can even auto-adjust rotor speed, extrusion torque, or cooling cycles based on the input plastic’s thickness and melt flow index. This reduces operator intervention, minimizes energy waste, and extends the lifespan of machine components.
By embracing intelligent automation, recycling plants can scale faster, adapt to material variability, and increase profit margins.
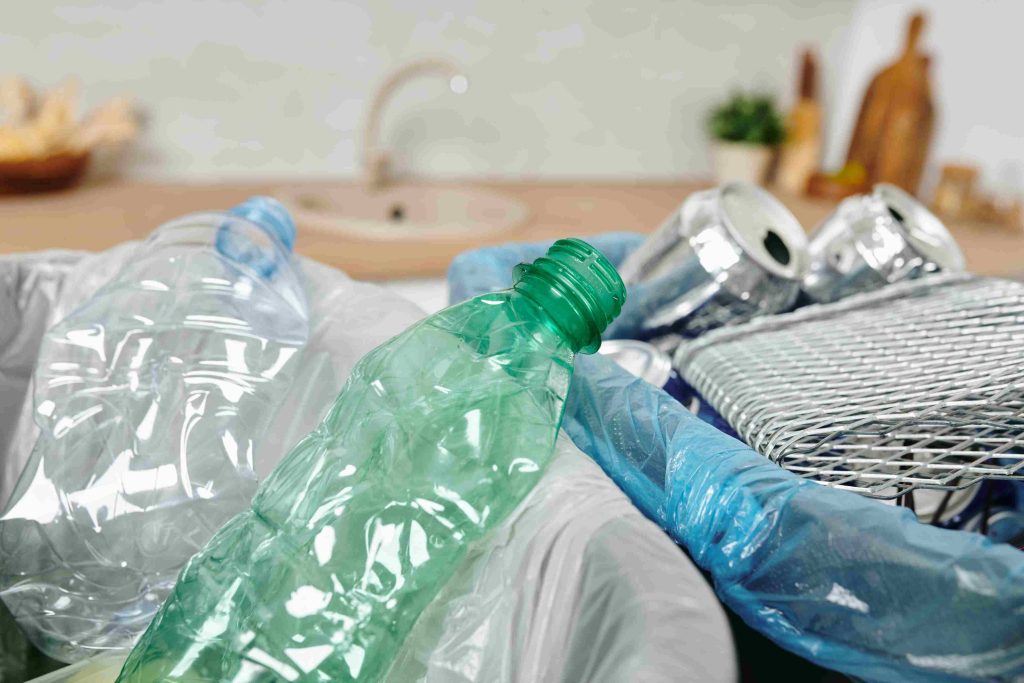
Why It All Matters: A Circular Future
It’s tempting to think of recycling as a side activity—something “green” companies do to look good. But that’s an outdated view. Today, plastic recycling is:
- A regulatory necessity in many countries
- A cost-saving measure for manufacturers
- A strategic advantage for brands marketing sustainability
- A supply chain stabilizer in times of raw material shortage
For businesses, investing in an in-house recycling line—equipped with a plastic crusher, low-temp granulator, and automated controls—means less reliance on virgin plastics, faster turnaround times, and lower costs.
In fact, more factories are integrating on-site recycling systems directly into their production lines. Waste from trimming, molding, or packaging can be ground and recycled back into the same process, creating a closed-loop system that’s both efficient and sustainable.
Real-World Applications: Where the Science Meets Industry
These advancements aren’t just happening in labs—they’re being deployed across industries:
- Packaging manufacturers are using low-temp granulators to recycle multilayer films.
- Automotive suppliers are reprocessing ABS and polypropylene from rejected parts.
- Construction firms are crushing PVC pipe offcuts for reuse in fittings and sheets.
- Electronics brands are reclaiming clean HDPE from damaged casings.
In each of these cases, precise, high-efficiency equipment is key. Machines must handle various polymer types, adapt to changing waste streams, and minimize energy consumption.
And they must do all of this without compromising product quality—a challenge that modern equipment is increasingly designed to meet.
Final Thoughts: Science in Motion
Recycling is more than a feel-good concept. It’s a science-based, machine-enabled process that transforms waste into value. With the right mix of chemistry, engineering, and intelligent automation, what once filled our landfills is now fueling our factories.
Soft-spoken but powerful, the machines that crush, wash, and reprocess plastic are the silent engines of sustainability. They don’t grab headlines—but they are reshaping how materials flow through our world.
As industries lean deeper into circular production, these machines will only become more essential. Because the future of plastic isn’t just in what we make—it’s in how we remake it