When only a milliliter makes a difference in the outcomes of the industry, as is the case in pharmaceuticals, cosmetics, and diagnostics, packaging accuracy is of paramount importance. With more complex product formulations and more precise consumer demands, manufacturers are increasingly being pressured to guarantee that each and every dose is measured, sealed and labeled to the finest of detail.
This is where the high technology packaging comes in. The spotlight falls especially on glass vials, which serve as secure vessels for sensitive liquids, and on the labeling machines that guarantee regulatory compliance, traceability, and brand consistency.
Sterile drug dispensing, specialty serums and perfumes, glass vial packaging, with automated labeling options, means that each product is delivered to its destination in an immaculate condition. In this article, we will discuss how these technologies come together to provide unrivaled precision and performance, even to the last drop.
Glass Vials: Trusted Containers in Pharma, Beauty, and Beyond
Glass vials are a mainstay in industries where product integrity cannot be compromised. Manufactured with borosilicate or soda-lime glass, the small containers are highly resistant to chemicals and clear or transparent and do not react, which makes it suitable to store injectable drugs, diagnostic reagents, vaccines, essential oils and high-quality cosmetics.
In pharmaceutical settings, glass vials are used extensively due to their ability to maintain sterility and prevent leaching or contamination. They can usually be used with many types of closure such as crimped aluminum caps, rubber stoppers, or plastic screw tops. Such flexibility can accommodate various applications- including single-use vaccine doses, and multi-dose medications.
In cosmetics and personal care, glass vials convey a sense of elegance and purity. Their transparency and smooth finishing make them more appealing to the eyes, and their durability makes them safe to use during transportation and storage of the products.
Despite their strengths, glass vials pose unique packaging challenges. They are delicate in their nature and cannot be handled carelessly, and their small size does not allow any labeling mistake. This is where specialized equipment such as vial fillers, capping units, and labeling machines become essential.
Whether used in aseptic manufacturing environments or boutique beauty labs, glass vials continue to set the gold standard for safe, attractive, and high-quality packaging.
Labeling Machines: Ensuring Consistency, Compliance, and Brand Identity
Labeling is more than a decoration, it is an essential process which closes the gap between regulatory, brand messages, and consumer trust. A labeling machine helps to label the right container, in the right location, and at the right time, without reducing efficiency.
For glass vials, labeling is particularly sensitive. They are cylindrical with small surfaces that need a lot of accuracy in label positioning as well as adhesion. Manual labeling also poses the dangers of the loss of the labels, wrinkles, and irregular application which might cause regulatory fines or brand degradation. That’s why automated labeling machines are the preferred choice for vial packaging lines.
Modern labeling machines come equipped with high-resolution sensors and servo motors that align and apply labels with incredible accuracy. They are capable of accommodating roll-fed labels, shrink sleeves or wrap-around types according to the size and form of the vial. These machines also read barcodes, text alignment and tamper-evident seals in real-time and are fitted with built-in vision systems.
FDA, EU and WHO labeling regulations are not negotiable in pharmaceutical packaging. Labeling machines ensure that critical information—such as lot numbers, expiration dates, and dosage instructions—is applied clearly and legibly on each vial.
To the beauty brands, the labeling machine will be an instrument of identity. It enables the application of custom designs, metallic finishes, and haptic decorations to be consistent, strengthening the feeling of luxury and confidence.
Regardless of whether it is regulatory traceability or visual branding, the labeling machine performs a critical role in providing both utility as well as visual polish.
Synchronizing Filling, Capping, and Labeling for Seamless Production
An efficient line to pack vials into a package is a ballet of precision machines-all working in harmony to their part. These processes should work together, like filling to capping and labeling, to guarantee quality, speed and sterility.
The sequence begins with volumetric or peristaltic filling machines, which dispense precise quantities of liquid into sterilized glass vials. Fill levels are verified by sensor-based systems and any underfilled or overfilled containers are rejected. The capping machine then places rubber stoppers and aluminum foils, which are usually crimped using crimping equipment to make them tamper-proof and sterile.
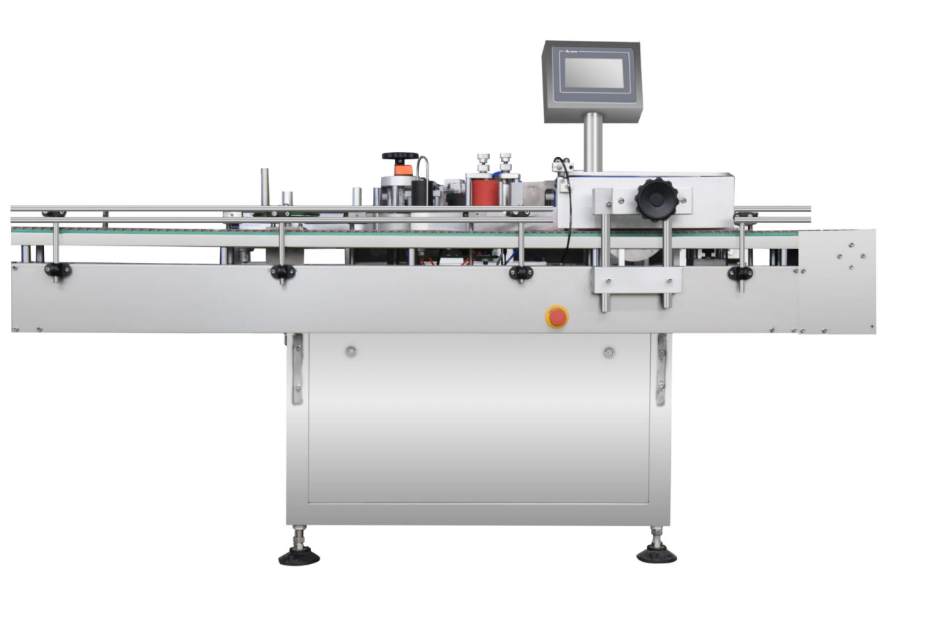
Next is the labeling machine which fits perfectly with the upstream equipment. With the help of timing belts, vision alignment, and PLC synchronization, it allows applying labels only to approved vials. Any vials that do not pass fill or seal inspection are automatically diverted- preserving the integrity of the product stream.
Common optional lines on automated lines are inkjet printers (variable data), shrink tunnels (tamper-evident seals), and secondary packaging (cartoning or tray packing). The effectiveness of these lines depends on intelligent incorporation, real-time diagnostics and adaptive controls.
Challenges and Innovations in Handling Fragile Containers:
Handling glass vials on automated lines presents a set of unique challenges. They are easily broken or fractured in high-velocity functions causing expensive loss of time, risk of contamination and wastage of materials. Moreover, they are lightweight and have a round shape hence proper feeding, alignment, and labeling is a technical challenge.
Machine design innovation has advanced to counter such problems. As an example, conveyance systems that are vibration-free and cushioned star wheels are used to minimize breakage on transfer. Pick-and-place systems can be gentle (and fast and accurate) with the use of robotics and vision.