In recent years, 3D printing technology has revolutionized the world of manufacturing, offering a transformative approach to modern production. 3D printing, also called additive manufacturing, creates three-dimensional objects from digital files. It is reshaping industries such as automotive, healthcare, fashion, and aerospace. This technology changes how products are made. It improves efficiency, reduces costs, and enhances customization in manufacturing worldwide.
The Basics of 3D Printing Technology
At its core, 3D printing technology works by layering materials (such as plastic, metal, or resin) to build up a physical object from a digital model. Unlike traditional subtractive manufacturing, 3D printing adds material layer by layer to form the desired shape. This process is highly versatile and allows for the production of complex geometries that would be impossible or highly expensive with conventional methods.
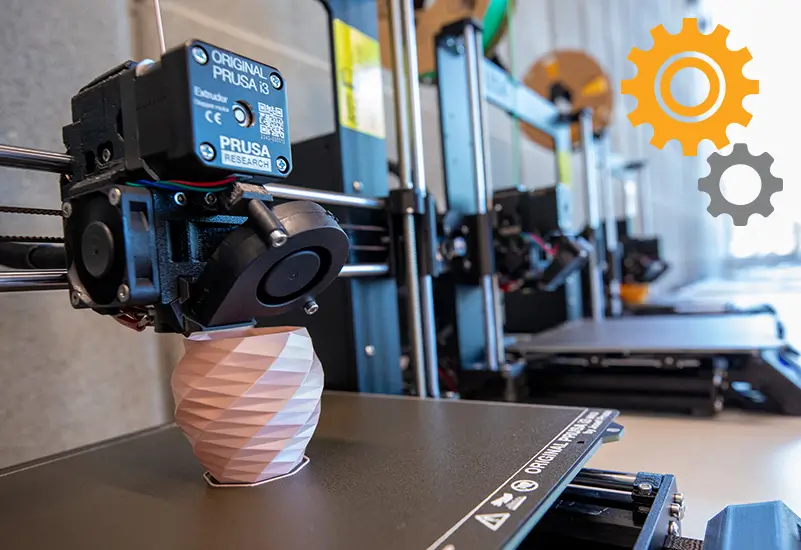
3D Printing: Enhancing Customization and Personalization
One of the key advantages of 3D printing technology in modern production is its ability to enable customization. Traditional manufacturing methods typically require molds or tooling that are expensive and time-consuming to produce. With 3D printing, however, companies can easily modify their designs or create bespoke products for individual customers without significant additional costs.
In healthcare, 3D printing technology creates customized prosthetics, implants, and even surgical tools. This level of personalization improves both the functionality and comfort of medical devices. Similarly, in the fashion industry, 3D printing allows designers to craft unique, made-to-order pieces, offering consumers greater individuality in their fashion choices.
Speeding Up Prototyping and Product Development
The traditional approach to prototyping involves creating physical models using subtractive methods, which can take weeks or even months. With 3D printing technology, however, prototypes can be produced in a matter of hours, significantly speeding up the product development cycle. This speed allows companies to test and iterate designs more efficiently, ultimately reducing time-to-market for new products.
3D printing’s rapid prototyping capabilities suit industries that require constant innovation, like automotive and consumer electronics. Designers and engineers can quickly modify prototypes. They can test them to ensure the final product meets specifications and performance requirements before mass production begins.
Reducing Costs and Material Waste
Another major benefit of 3D printing technology is its ability to lower production costs and reduce material waste. Traditional manufacturing methods often involve cutting or machining large blocks of material, which results in a significant amount of waste. In contrast, 3D printing only uses the material needed for the object, minimizing waste and lowering material costs.
In addition to material savings, 3D printing technology can also reduce labor and tooling costs. The process is largely automated and doesn’t require expensive molds or tooling. As a result, companies save on manufacturing setup costs and labor expenses. For small-batch or custom production, 3D printing is often more cost-effective than traditional methods. Traditional manufacturing equipment requires a significant upfront investment.
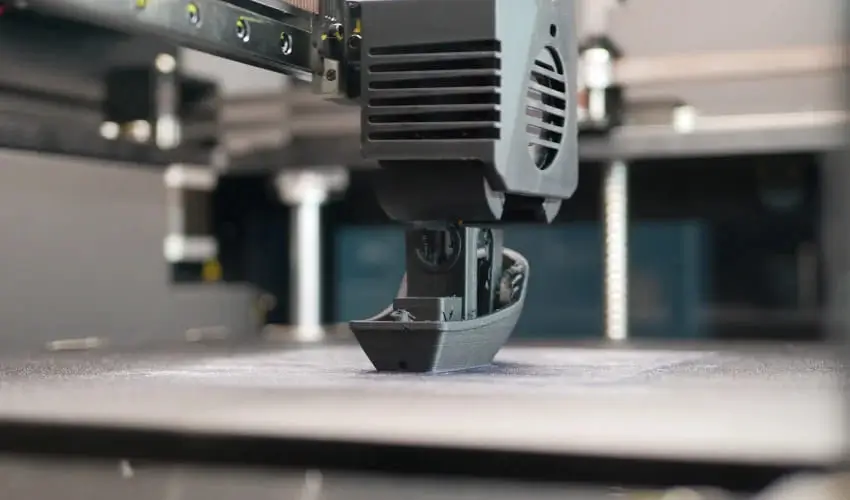
Supporting Complex and Lightweight Designs
In industries like aerospace and automotive manufacturing, where weight and material efficiency are critical, 3D printing technology is a game-changer. The technology enables the creation of lightweight, complex structures that would be difficult or impossible to achieve with traditional manufacturing techniques. For instance, manufacturers can produce aircraft components with intricate lattice structures that reduce weight without compromising strength, leading to fuel savings and enhanced performance.
In the automotive industry, 3D printing technology allows for the production of lightweight parts that contribute to vehicle efficiency and reduced emissions. Furthermore, designers can integrate multiple functions into a single component, streamlining the production process and reducing the number of parts required.
Transforming Supply Chains and On-Demand Production
3D printing technology is also reshaping traditional supply chains. With the ability to produce parts and products on demand, companies can reduce their reliance on overseas manufacturing and minimize the need for large inventories. This approach, known as “just-in-time” manufacturing, allows businesses to produce parts locally, reducing shipping costs and lead times while also making supply chains more flexible and responsive to market demands.
Moreover, 3D printing technology makes it easier to manufacture spare parts on demand, addressing the challenges of sourcing hard-to-find components. In industries like aerospace and automotive, on-demand production via 3D printing allows companies to carry out repairs and maintenance with minimal downtime, reducing the time and cost of sourcing expensive spare parts.
3D Printing Technology: Paving the Way for Sustainable Manufacturing
As industries worldwide focus on sustainability, 3D printing technology is emerging as a more eco-friendly alternative to traditional manufacturing methods. By reducing material waste, minimizing the need for transportation, and enabling local production, 3D printing contributes to lower carbon footprints and more sustainable production practices.
The use of recyclable materials in 3D printing technology also supports eco-conscious manufacturing. Many companies are exploring biodegradable and recyclable filament options, further enhancing the sustainability of additive manufacturing. Additionally, because 3D printing allows for the efficient use of materials, it reduces the need for excessive raw material extraction and contributes to a more sustainable supply chain.
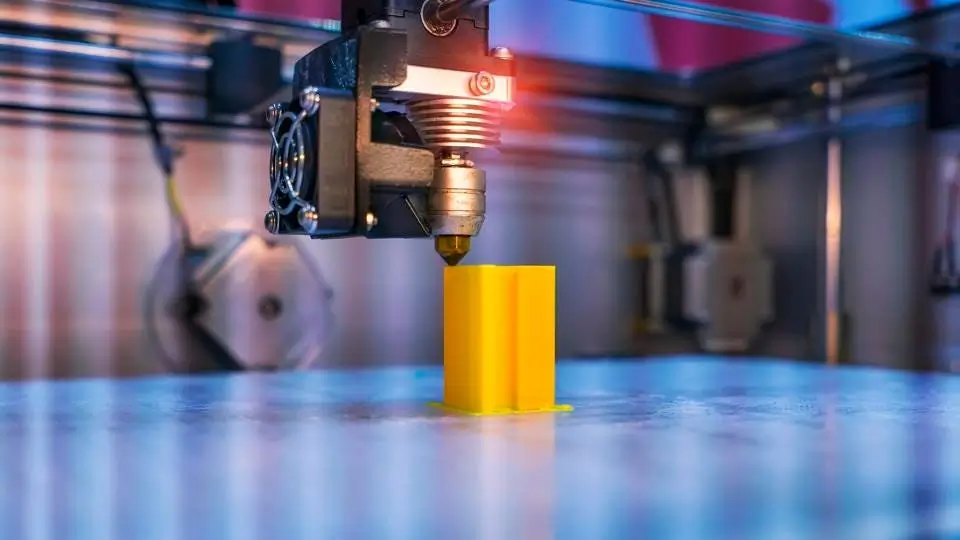
The Future of 3D Printing Technology in Production
Looking ahead, the potential for 3D printing technology in modern production is vast. As technology evolves, it will drive advancements in industries like healthcare, aerospace, automotive, and consumer goods. In the near future, 3D printing could create entire buildings. Large-scale 3D printers will print structural components on-site. New materials and faster printing speeds will enhance 3D printing’s capabilities. This will make it even more integrated into mainstream manufacturing.
With advancements in artificial intelligence, machine learning, and robotics, the process of 3D printing technology is becoming more automated and efficient. These technologies will integrate to enable faster production times, improve quality control, and create more sophisticated designs, further pushing the boundaries of what additive manufacturing can achieve.
Conclusion
The power of 3D printing technology in modern production is undeniable. 3D printing enhances customization and reduces costs. It enables faster prototyping and supports more sustainable manufacturing. This transformative technology is reshaping industries worldwide. As it evolves, its potential to revolutionize manufacturing grows. Moreover, 3D printing technology is also being applied to medical development. Let’s look forward to its technological breakthroughs in cardiac care technology. It offers exciting possibilities for innovation and efficiency. The future of 3D printing is bright, and its impact on production will last for years.